Industrial safety
AREA, STRATEGIC GOALS AND HIGHLIGHTS OF 2023In accordance with the materiality principle, the quantitative metrics in this section are presented for Apatit (Boundary 2) (Apatit is a subsidiary of PhosAgro holding its production assets)
Target 3.4
Reducing risks of traffic accidents
Target 3.4 и 8.8
Fostering a safety culture and adhering to the highest occupational health and safety standards
Reducing workplace injuries by 10% annuallyIn accordance with the materiality principle, the quantitative metrics in this section are presented for Apatit (Boundary 2) (Apatit is a subsidiary of PhosAgro holding its production assets)
Zero fatalities, and reducing the number of incidents by 10% annually
Target 4.4 и 8.8
Improving safety competencies
Keeping employees motivated to stay safe and protect others
Target 3.4
Disease prevention and health improvement among the employees of all production sites
Providing employees with access to high‑quality affordable healthcare
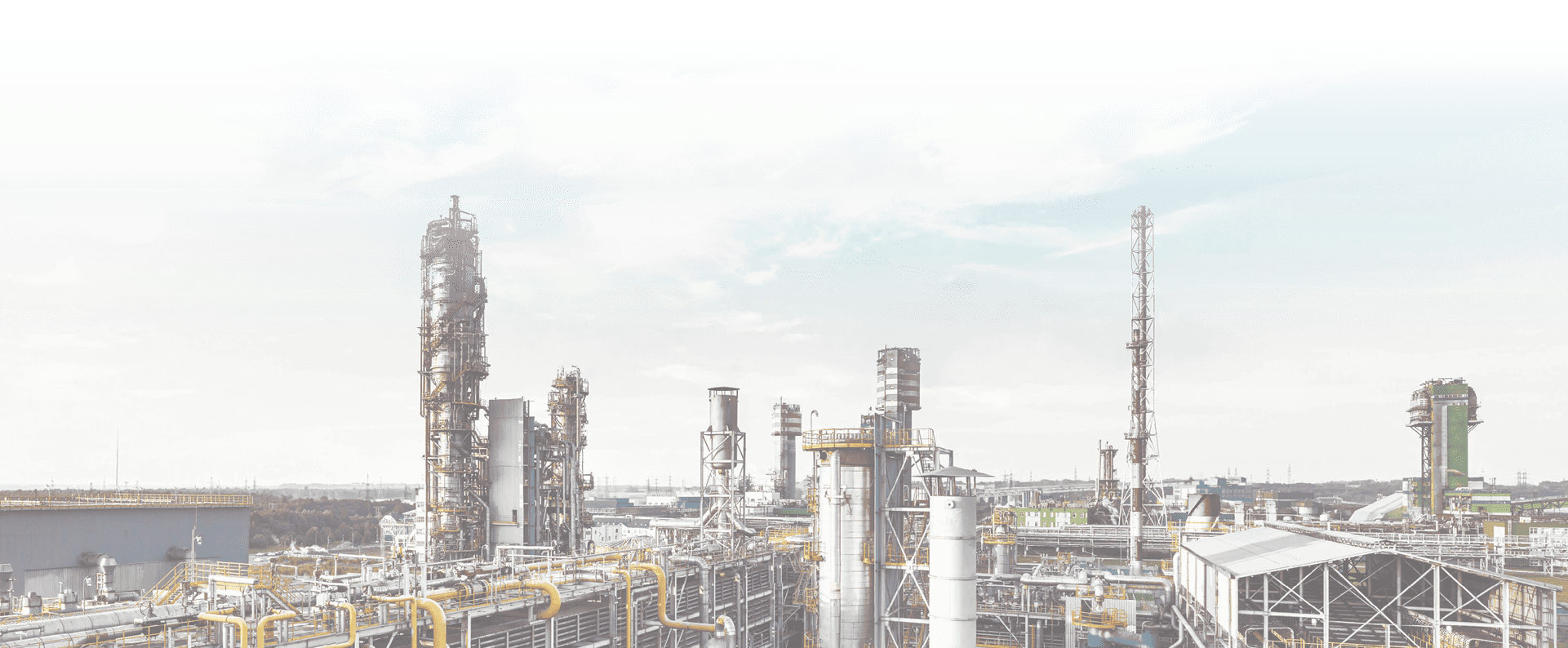
All employees of PhosAgro Group and its contractors need to go back from work to their loved ones in perfect health. This is the underlying principle of all our efforts to ensure safe, healthy and comfortable workplace conditions.
Our Strategy to 2025 focuses on fostering a safety culture and adhering to the highest occupational health and safety standards. In 2023, we continued to implement our Health and Safety Strategy, which defines key focus areas and target initiatives to reduce the risks associated with various operations.
The Company’s relevant goals and objectives, both strategic and day‑to‑day, are based on huge volumes of data derived from internal and external audits, inspections, incident investigations, employee recommendations and feedback.
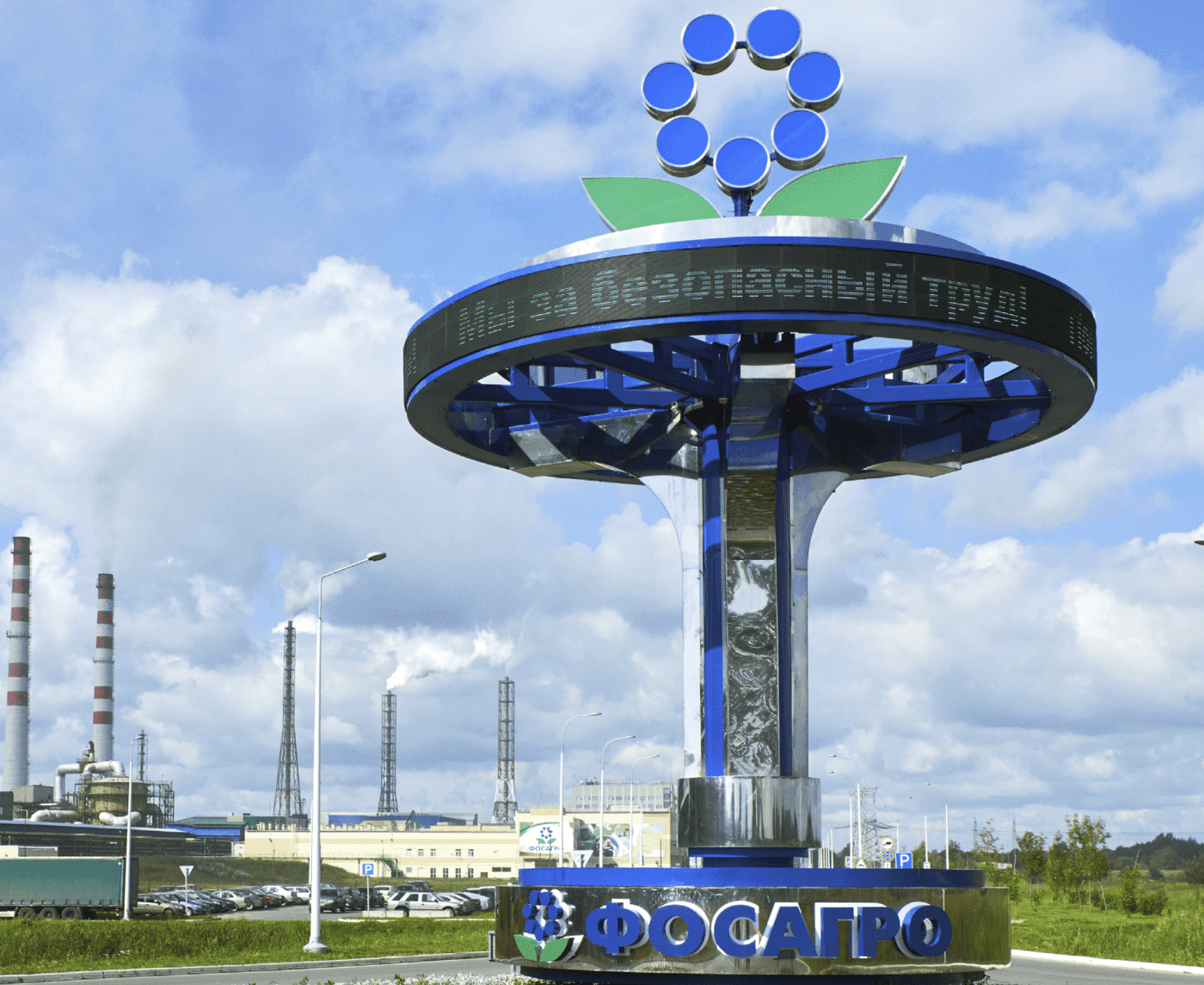
PhosAgro Group is consistently improving its safety culture, employee responsibility and awareness, hazard identification procedures and danger prevention measures by putting managers at all levels in charge and studying and applying best health and safety practices. We apply continuous efforts to identify and reduce health and safety threats to PhosAgro Group employees, contractors and visitors to the Company’s sites.
We pay special attention to making our health and safety system compliant with applicable laws and the highest international standards.
To this end, we have introduced a multi‑tier health and safety management system involving managers of all levels. In 2008, the Company introduced an integrated health and safety management system in line with BS OHSAS 18001. In 2021, Apatit’s Cherepovets site was certified and successfully audited for compliance with ISO 45001:2018 in 2023.
Occupational health functions play a key role in ensuring safety at our facilities.
Their main objectives are:
- taking steps to ensure compliance with OHS requirements by workers and third parties;
- monitoring workers’ compliance with OHS laws and regulations, the Collective Bargaining Agreement, OHS agreement and other internal regulations;
- preventing workplace injuries, occupational diseases and improving workplace conditions;
- advising workers and contractors on, and raising their awareness about, occupational health and safety;
- studying and promoting best OHS practices.
Apart from applicable laws, these activities are regulated by:
- health and safety SOPs at the facility (shop) level;
- production SOPs;
- worker health and safety instructions;
- corporate standards;
- process regulations;
- accident management action plans, etc.
For better OHS communication with employees, we have adopted the Regulations on the OHS Communication System. Pursuant to the Regulations, the OHS communication system is divided into internal and external communications, and provides for a feedback procedure:
- regular OHS meetings at business units and enterprises;
- OHS meetings at production sites, departments and facilities;
- union and union committee meetings (for feedback from OHS officers);
- corporate e‑mail;
- corporate periodicals;
- local health and safety committees;
- employee loyalty surveys;
- OHS questionnaires.
Internal OHS communication is achieved through:
- local health and safety committees;
- management meetings and conferences to discuss the health and safety performance of our enterprises;
- regular OHS meetings in departments, on production sites and at facilities;
- health and safety bulletin boards, posters and other visuals;
- corporate television (screens), intranet site, e‑mail;
- corporate periodicals;
- education by OHS officers (including one‑on‑one meetings, training, mentoring, supervision, etc.).
Local health and safety committees
Since 2014, health and safety committees have been functioning at the Group’s companies. They are both an integral part of our OHS management system and a form of employee participation in it. In their work, these committees rely on the principles of social partnership. As part of their activities, health and safety committees draft and improve programmes to join efforts of the employer, employees and trade unions in ensuring occupational health and safety.
Committee meetings are held at least once a month and chaired by heads of companies. At meetings, information exchange and reporting are multilateral, as both health and safety functions and local unit heads report on health and safety progress. All resolutions are documented in minutes of the meetings.
As part of these workstreams health and safety committees consider the following topics:
- “Golden Rules” of OHS;
- Safety Culture Transformation Project;
- OHS leadership;
- OHS motivation;
- effective OHS communications;
- contractors’ safety;
- PPE effectiveness;
- trade union report.
Workers are represented at committee meetings by heads or representatives of local unions.
Meeting agendas comprise nine workstreams
Improving contractor safety practices
Measures to ensure safety of contractors’ employees working at our production and other facilities are an integral component of our OHS strategy. They include the selection of contractors based on a health and safety qualification assessment, briefings, enforcing their application of our safety tools, and conducting relevant OHS compliance audits.
ESG assessment is a key factor in contractor selection.
for more information, see the Supply Chain section
Internal and external industrial safety audits
In line with statutory requirements, PhosAgro Group is subject to scheduled external audits by Russian authorities, including the Federal Service for the Supervision of Environment, Technology and Nuclear Management (Rostekhnadzor), State Labour Inspectorate, Federal Service for Surveillance on Consumer Rights Protection and Human Wellbeing (Rospotrebnadzor), the Ministry for Civil Defence, Emergencies and Elimination of Consequences of Natural Disasters (EMERCOM), etc. We may also engage consulting companies, or international associations of which the Group is a member to conduct additional external audits of compliance with international standards, or as part of a special assessment of workplace conditions.
We also run internal audits conducted by our OHS departments and directorate, managers and employees exercising production H&S control.
After external and internal audits, the Company issues orders and instructions outlining remedial action plans and establishing the deadlines and responsible persons. Identified breaches are remedied within the agreed time limits.
The Company has a procedure for drafting, submitting and reviewing reports on internal and external OHS audits. The results of all internal and external assessments and audits are recorded in the Safety and Instructions (Shift Assignments) management systems offering instruments for further analysis, gap identification, and elimination monitoring. We also submit all relevant reports to state supervisory bodies and statistical agencies in accordance with the Russian laws.
The following strategic risks affect our OHS objectives:
for more information, see the Strategic Risks section
OHS‑specific risks
We are constantly working to assess and mitigate risks. We perform risk assessment and classify them by severity and frequency using our dedicated proprietary methodology. Following hazard identification and risk assessment, the unit’s OHS officer compiles a List of Occupational Risks, which is then used as a basis for the Company’s List of Material Occupational Risks.
Risk assessment takes into account the following aspects:
- degree of personnel exposure;
- impact on personnel;
- frequency of occurrence;
- compliance with the applicable regulatory and other OHS requirements.
The Company has instituted a robust protocol that facilitates swift communication from eyewitnesses to the appropriate functions and managerial personnel, inclusive of PhosAgro’s CEO by means of corporate communication tools such as text message alerts and telephone calls.
All incidents are investigated in accordance with legislative requirements and internal procedures to determine the root causes. The Company encourages its staff to disclose information on potential sources of danger to worker health and life.
For better OHS efficiency, and to automate and streamline the relevant processes, we have introduced and now use the Safety and Instructions (Shift Assignments) management systems. Both systems include a Risk Management module. The module enables internal check list‑based OHS assessment at all units of Apatit. The module’s new underlying principles help enhance production H&S control, while its new functions facilitate operation, monitoring and analysis.
The Company has a formal procedure for addressing workplace hazards. When a hazard is identified, employees are required to suspend work and report it to their supervisors directly or via the Public Scrutiny mobile app (on an anonymous basis if necessary). The supervisor uses the report to assess the risk and develop a remedial action plan.
Emergency response procedures
At our sites, we have introduced the following emergency response and prevention measures compliant with the Russian laws:
- accident management action plans for all hazardous industrial facilities as defined by the Russian laws developed;
- training sessions and drills held in 2023:
- test alerts – 143,
- fire training sessions – 636,
- evacuation drills – 132,
- joint fire drills with EMERCOM – 5;
- a targeted programme for upgrading Apatit’s fire safety systems in 2023–2025 developed.
Project
to roll out the OHS remote monitoring system at the Cherepovets site of Apatit
The Company endorses the initiatives put forth by state authorities as regards OHS data disclosure, in order to facilitate remote monitoring measures and alleviate the regulatory oversight burden.
Starting from 2021, Apatit’s Cherepovets site (fluosilicate acid storage facility of the aluminium fluoride shop) participates in Rostechnadzor’s experiment to roll out an OHS remote monitoring system under Russian Government Decree No. 2415 On Experimental Roll‑out of the Industrial Safety Remote Monitoring System dated 31 December 2020. The experiment provides for the development of stand‑alone remote monitoring technology for hazardous production facilities, and a relevant legal framework. The technology is expected to improve the overall reliability and monitoring efficiency of safety systems, and help reduce the associated paperwork and bureaucracy.
The OHS remote monitoring system was put into operation in April 2023, with the process of data transmission to the Automated Information System of Rostekhnadzor configured.
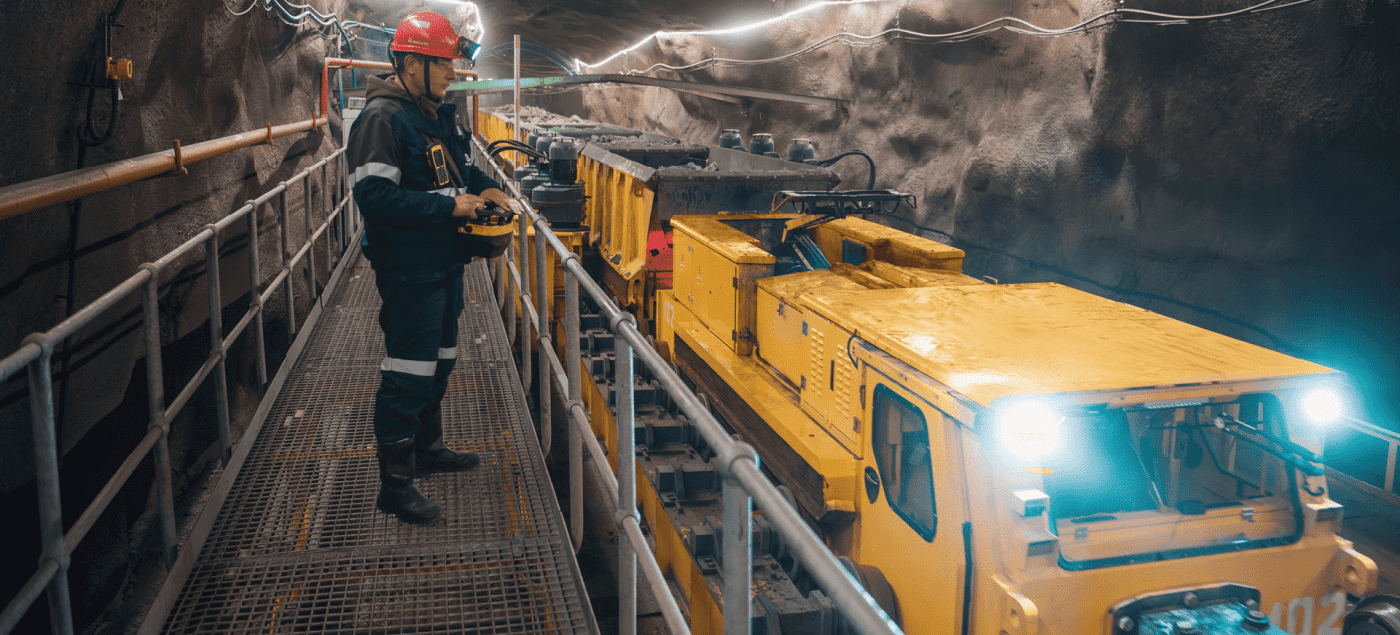
The solid increase in OHS expenses is attributable to higher investments in personal protective equipment and training in modern OHS practices for employees. Moreover, the ramp‑up of production along with the initiation of upgrade and revamp projects triggered the recruitment of extra staff. This contributed to an uptick in overall OHS spending. Specifically, there were heightened expenses for check‑ups, establishment of supplementary fire command stations (fire brigades), and engagement of services from professional rescue squads.
From 2021 to 2023, PhosAgro Group was able to reduce the total number of traffic accidents nearly fivefold (by 78%) from 37 accidents in 2021 to eight in 2023.
The initiatives implemented by the OHS Department and transport departments to mitigate traffic accident risks includes drafting internal regulations to ensure safe operation of motor vehicles, self‑propelled machines and rail transport, performing targeted and full‑scope inspections of vehicles used by our contractors, subsidiaries, enhancing the competencies and skills of PhosAgro employees responsible for operating all types of transport, and introducing various technical solutions to mitigate risks of traffic accidents. For instance, the Kirovsk branch equipped quarry self‑propelled machines with visualisation systems for dangerous zones. There are also ongoing pilot tests for similar systems in underground operations, as well as for collision prevention systems on quarry dump trucks. Preparations are underway at the Cherepovets facility and the Balakovo branch to outfit dump trucks with a fatigue monitoring system tailored to help drivers during their 12‑hour shifts. Additionally, the Kirovsk branch holds annual training sessions under the Safe Driving programme, and a driving skills competition for dump truck operators.
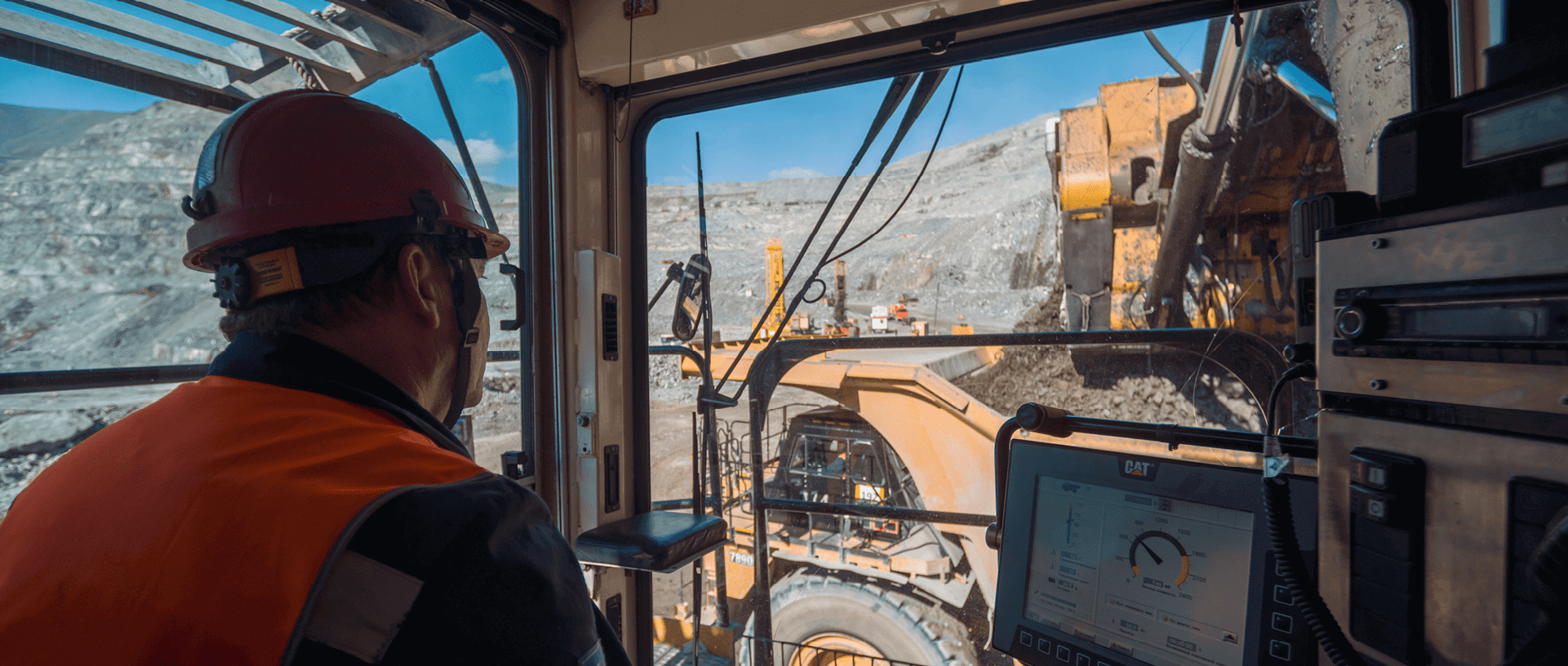
There were no fatalities across the Company’s facilities, but the total number of work‑related injuries, both minor and severe, increased. At the time of publishing this Report, an official investigation is being conducted into an incident involving a Company employee in 2023. The incident has been categorised in the Report as a severe injury, but it is subject to potential reclassification based on the investigation findings. The was a total of 33 injuries recorded in 2023 compared to 20 in 2022. Of these injuries, nine occurred to contractor employees, nine to PhosAgro’s own staff, and 15 to employees of subsidiaries and affiliates (compared to five, eight, and seven in 2022, respectively), which accounted for the largest proportion of all work‑related injuries, including major accidents. We are convinced that rolling out the existing methods and tools in the field of occupational safety among personnel of contractors, as well as subsidiaries, affiliates and managed companies, will further reduce the level of occupational injuries among this category of personnel.
Most of the injuries reported in 2023 were related to falls and contact with moving and rotating objects and equipment, as well as impact of hazardous substances.
The main causes of work‑related injuries in 2023 were poor work organisation, violations of labour and industrial discipline, personal negligence, and underestimation of risks by the injured persons.
- senior management’s leadership and commitment to health and safety;
- allocating sufficient funding to ensure occupational, industrial and fire safety;
- knowing and applying international and domestic best practices;
- improving the internal incident investigation process to identify and eliminate root causes;
- implementing project solutions and targeted programmes to improve workplace safety;
- providing employees with modern and effective personal and collective protective equipment;
- involving blue‑collar workers (OHS officers) in directly managing health and safety in their business units;
- reviewing the structure and functions of occupational health, industrial safety and fire safety services with a focus on enhancing control and preventive work;
- selecting and appointing highly qualified leaders to key positions in occupational health, industrial safety and fire safety services;
- developing and implementing a system of incentives motivating all categories of employees for safe working practices;
- developing and updating e‑courses to educate employees in corporate health and safety requirements;
- integrating corporate health and safety requirements into the work of contractors;
- digitalising data management processes to support high‑quality analysis and effective management decision‑making.
The Company offers continuous education for employees, conducts workshops and trainings.
- Safe Behaviour Fundamentals – in‑person training for new hires and employees of business units where accidents have occurred, with the focus on risk identification and management methods
- Training of the Company’s and contractors’ staff on working at heights
- The Rules – a training for white‑ and blue‑collar workers in the modern methods to raise employees ’ awareness of safety rules
- Golden Rules – training the Company’s (online training) and contractors’ (workplace training) employees.
PhosAgro makes efforts to improve OHS competencies and knowledge of its staff. Employees of the Company undergo online and in‑person training. Our e‑courses are easy to understand since they are made in the form of illustrated slides with key highlights on them. In particular, we offer an e‑course on corporate OHS standards. It is followed by tests to check the knowledge and understanding of the standards and requirements.
Whenever required, the courses developed earlier are updated following changes in the law and the Company’s internal regulations. In 2023, we developed and updated the following e‑courses:
- operation and maintenance of Apatit’s rail infrastructure;
- organising and exercising production H&S control at Apatit’s hazardous facilities;
Employees undergo OHS training, including that in basic fire safety and electrical safety, industrial safety pre‑certification sessions, and drills in the Vysota training centre.
All our employees, from managers to blue‑collar staff, receive occupational health and safety briefing and training as required by the Russian laws. Furthermore, the employees of the Company and some contractors are offered a number of additional courses.
We use animated videos to improve OHS training and remind employees about workplace safety.
Raising awareness about OHS
To keep our employees well‑informed about our safety measures, PhosAgro constantly develops and updates OHS check lists, presentations and other visual materials that emphasise the crucial information employees must rely on in various situations, including working on particular assignments, in order to stay safe.
Raising awareness about occupational health and safety, each month the Company issues check lists on the month’s topic. In 2023, such topics included the “Golden Rules” of OHS, use of PPE, safe behaviour, and high‑risk operations.
In the reporting year, the Company was actively carrying out briefings for each shift – daily OHS trainings for employees, revising industrial dangers/hazards, OHS requirements (as set out in the Company’s internal regulations, OHS guidelines, technical and operational documents), and safe work practices.
The key objectives of such briefings are:
fostering leadership skills among mid‑level managers;
developing managers’ communication skills;
obtaining employee feedback on safety issues;
maintaining direct communication between managers and their subordinate staff.
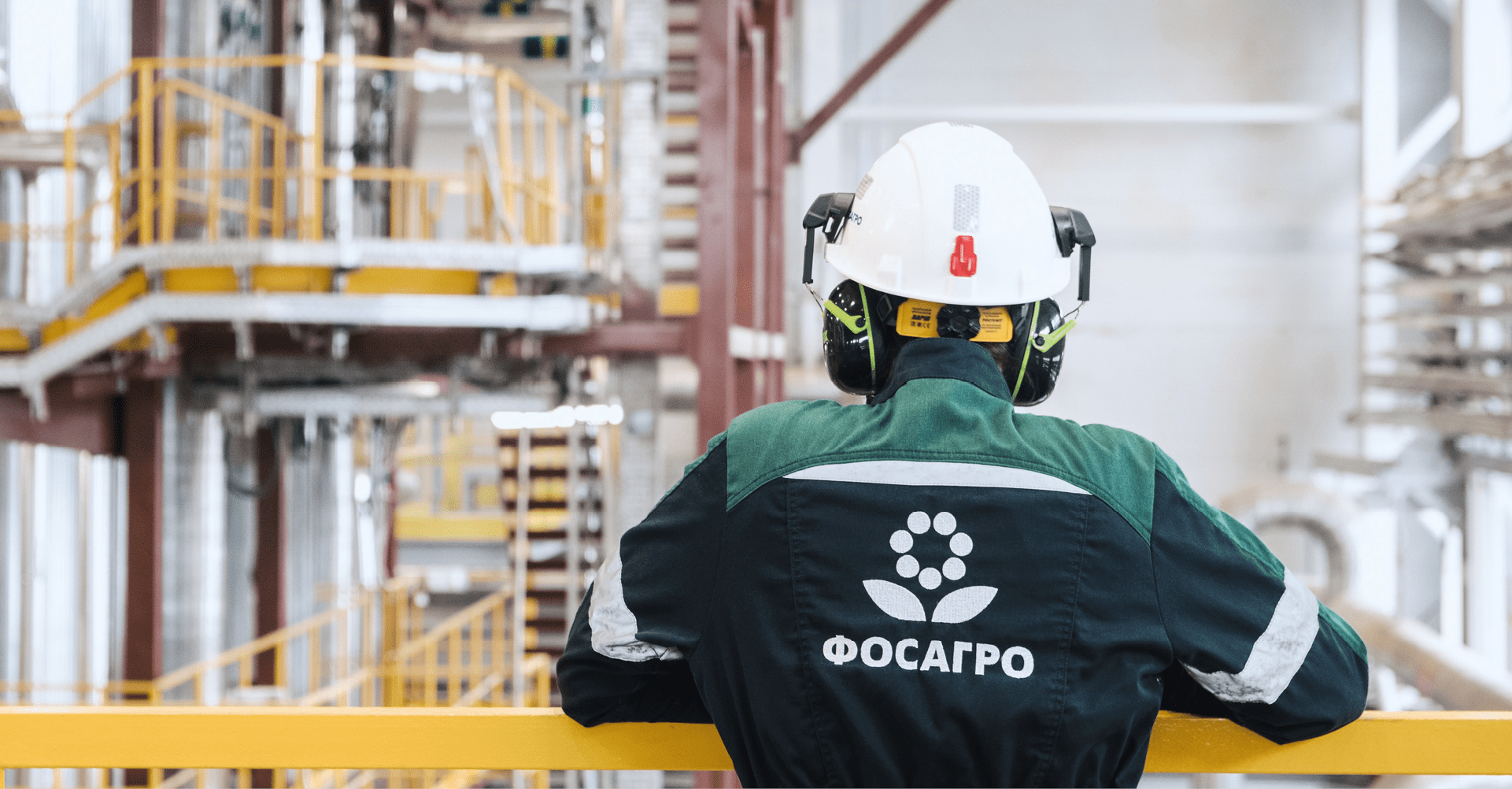
Changes to labour safety promotion programmes
Senior executives (CEOs of the Company and its business units, as well as their direct subordinates) recognise the importance of OHS and are committed to safety and ready to take necessary managerial decisions. Since 2014, PhosAgro has had a system of KPIs that uses uniform standards linking the size of management remuneration to the efficiency of OHS measures, among other things. In particular, the Company established the following KPIs with regard to OHS:
- LTIFR covering all staff categories, including contractors;
- zero fatalities among all employee categories, including contractors;
- timely implementation of action items from improvement notices issued by supervisory authorities.
The Company has developed OHS promotion programmes to maintain each PhosAgro employee’s engagement in ensuring their own safety and the safety of those around them, as well as to encourage the employees to take initiative and implement OHS improvements.
The incentive system includes both individual and collective programmes.
Individual incentive programmes (with results summarised quarterly):
Best OHS Employee
Safety Ideas
Best Public Scrutiny User
CEO’s OHS Achievement Award
Best OHS Business Unit
In addition, in 2023, occupational diseases were detected in two employees who work for subsidiaries and affiliates and perform their job duties at the Cherepovets facility and the Kirovsk branch of Apatit. The notable growth in the number of detected occupational diseases in 2023 compared to previous years is due to the introduction of in‑depth medical examinations at the occupational pathology centre.
PhosAgro places a strong emphasis on disease prevention, health improvement, and high‑quality affordable healthcare and prevention for the employees of its production sites.
The Company takes part in the Health 360 programme run by the Russian Chemists Union. In 2023:
- The Volkhov branch of Apatit was the runner‑up in the Wellness Culture Development nomination of Russian national contest dubbed Investing in the Development of a Healthy Country. Best Corporate Practices
- The Volkhov branch of Apatit won a leader diploma at Healthy Working Environment 2023, a contest of corporate health promotion programmes for employees in the Northwestern Federal District
- The Volkhov branch of Apatit took the third place in the Leningrad region Cup in Nordic walking
- Apatit was awarded a participant’s diploma in the Sports Culture Development nomination of Russian national contest dubbed Investing in the Development of a Healthy Country. Best Corporate Practices.
In 2023, the Company continued to expand its staff support programmes (mental health support, online advice for personal circumstances, etc.) and programmes to promote health and well‑being (telemedicine, healthy diets, emotional unwinding, etc.) to benefit more employees.
All employees who have signed an employment contract with the Company benefit from long‑term voluntary health insurance (VHI) covering an extended range of risks. Health insurance contracts are signed annually as part of long‑term cooperation with the SOGAZ insurance company.
The benefits include:
- health resort (rehabilitation) treatment at corporate resort centres in our regions of operation and countrywide;
- services of outpatient clinics and health posts (including those available 24/7) at the Company’s production sites, operated by corporate medical centres and private and state‑run healthcare facilities;
- treatment (expensive, dental, medical counselling) at healthcare facilities in our regions of operation and in other Russian regions.
On‑site clinics can provide accident and emergency care, as well as specialist advice. PhosAgro also has mobile medical teams and organises screening sessions for its employees.
Employees of all PhosAgro facilities enjoy access to Telemed, a telemedicine service offered by SOGAZ.
PhosAgro’s production sites organise initial and regular check‑ups and examinations of staff involved in potentially hazardous and/or dangerous activities.
Since 2010, the Company has been running a programme to improve social and working conditions by conducting annual scheduled repairs in all buildings housing social and sanitary facilities, canteens, and workplaces. PhosAgro invested over RUB 3 bln in this programme in 2013–2023.
In 2023, as part of initiative to improve working conditions, employees of Apatit business units in Cherepovets received modern, comfortable, and durable chairs selected following tests at business units and surveys in Apatit and its branches, with as many as 99 chairs replaced in workshops.
In 2023, the Company continued changing its menu of dietary and healthy meals provided to employees working in harmful conditions. Quality of the meals is subject to regular control in cooperation with the trade union.
Every day, each canteen at the Company’s facilities serves up to 800 people, and all meals are assessed each quarter based on employee surveys, review of complaints, and canteen attendance levels. Employees can comment on the quality of meals in a real‑time mode by completing a survey available in corporate canteens via a QR code. On top of that, we have a dedicated working group that attends all of Apatit’s sites to assess food quality and canteen conditions.
In 2021, PhosAgro started a pilot project to use a traffic light labelling system for foods as a way to promote healthy dieting among employees.
Employees of the Company and members of their families have access to corporate recreation centres and health resorts in Southern regions at a reduced price. In 2023, over 1,000 vouchers were granted for employees to spend their holidays at southern health resorts.
PhosAgro’s facilities have corporate fitness centres, which include game halls, gyms and swimming pools and are available to employees on a daily basis. The pool of our Cherepovets facility offers classes in water aerobics and swimming lessons, both very popular among employees. In 2023, over 25,000 people visited the Cherepovets sports and recreation facility.
An annual sports contest (Spartakiad) is held for employees in 18 sports with new sports introduced. Teams in football, volleyball, and other sports represent the Company in various levels of competitions, including national ones.
Since 2020, our production facilities provide free psychological support to employees, with in‑house psychologists available to them for counselling and advice. As part of the Employee Mental Health Support programme, the Company offers meetings in person, online interviews, and comprehensive events such as webinars, training sessions, and marathons to minimise conflicts in teams, improve psychological resilience, and increase performance. In 2023, on‑site psychologists received 3,257 requests from the Company’s employees.
We continue to extend our Psychological Relief Room, a project kicked off in 2021 at the Balakovo branch. In the reporting year, a plan was developed to roll out such rooms at the Cherepovets site.
In 2023, Healthy Lifestyle Mania, Apatit’s employee support programme designed to promote active lifestyles, physical and sports activities, and healthy nutrition among employees, gained traction among the staff of Apatit’s Balakovo branch.
To promote traditional spiritual values, improve social and psychological climate in the team, and enhance emotional well‑being, the Company does a lot to help build and reconstruct Orthodox churches.
Those employees whose children are involved in the DROZD project (Educated and Healthy Children of Russia) annually take part in several joint training sessions and sports contests held among families. At the DROZD sports facilities, our employees can work out and get ready for GTO (Ready for Labour and Defence) fitness tests.
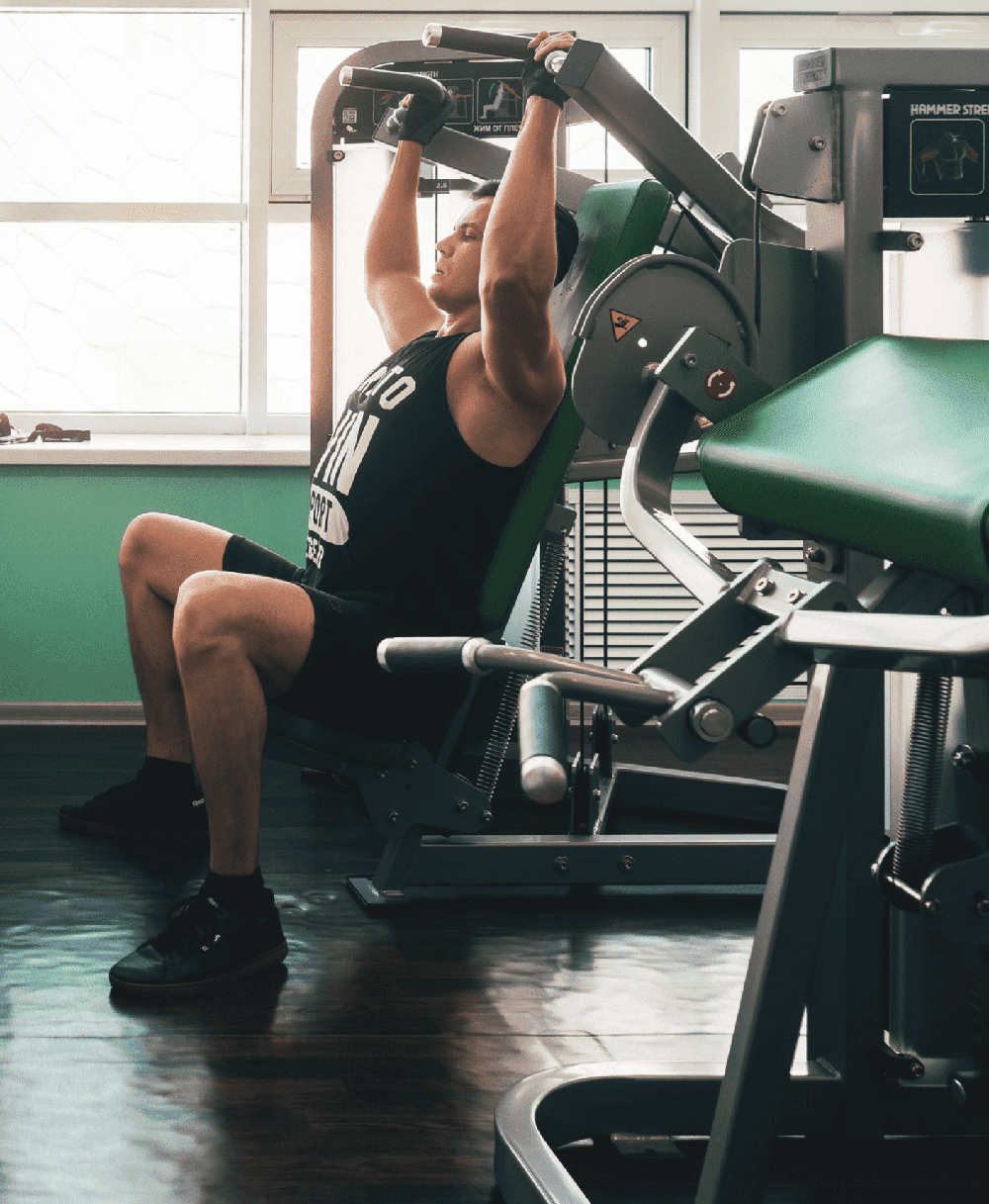
Targeted programme for upgrading Apatit’s fire safety systems in 2023–2025
In 2023, the facilities of the Cherepovets facility, Volkhov and Balakovo branches were audited for the availability and compliance of fire protection systems with the requirements of applicable rules and regulations.
Following the audit, we identified facilities in need of repair, replacement or installation of new automatic fire protection systems and carried out an initial assessment of the cost of the entire range of work to implement the target programme. The Company defined key requirements for the implementation of the targeted programme for upgrading Apatit’s fire safety systems, namely:
- the procedure for works in 2023 to implement the targeted programme at the facilities of Apatit and its branches;
- requirements for contracts with parties involved in the targeted programme;
- milestones for the whole period of the targeted programme implementation at the facilities of Apatit and its branches;
- the procedure for financing the targeted programme for upgrading Apatit’s fire safety systems.
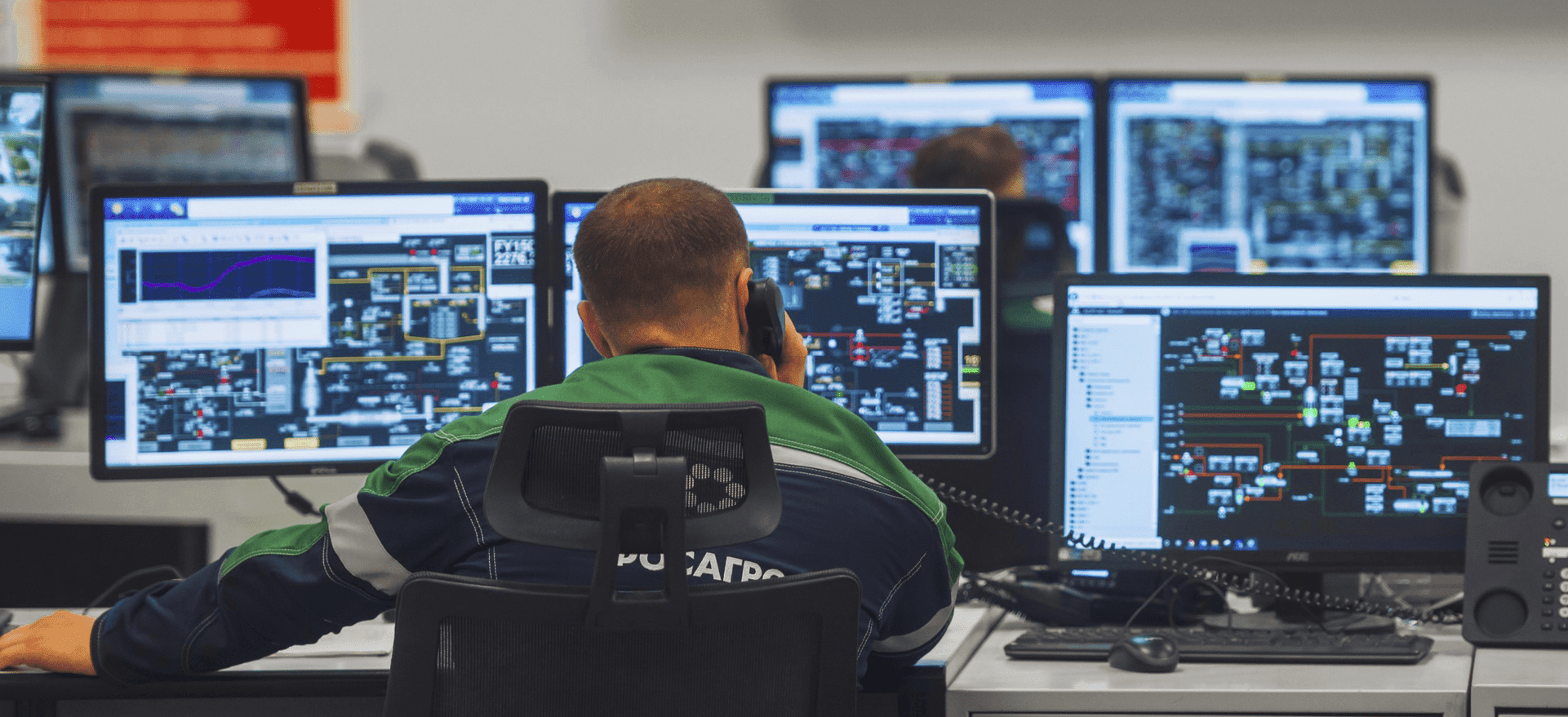
Transformation of safety culture and OHS management system
Since 2021, we have been running a project – Transformation of Safety Culture and OHS Management System – focused on switching to proactive OHS management.
Project goals:
- transforming the safety culture and developing OHS leadership;
- developing, adapting and ensuring the sustainability of best practices in the field of safety culture and OHS management improvements;
- learning how to arrange and carry out works associated with high OHS risks;
- ensuring the sustainability of our performance and the relevance of our management system over the next five years;
- reaching stage 3.1 as per Bradley curve (we are currently at stage 2.2).
The project covers key business units of Apatit, entities under management, subsidiaries and affiliates, and key third‑party contractors engaged by our production sites.
In 2023, as part of the Risk Hunting initiative, a total of 2,529 risks were identified, out of which 374 were classified as critical. Measures for elimination or mitigation were developed for each risk. By the end of 2023, 60% of the critical risks (224) were eliminated.
In 2023, we continued our efforts to implement, develop, and improve transformation tools.
Leadership visits – comprehensive study of business units by top executives of enterprises to jointly address identified risks and develop improvement actions.
Standard operating procedures – a step‑by‑step operating protocol for employees when performing work beyond the scope of high‑risk operations when servicing specific process equipment.
Risk hunting – engagement of managers at the business unit level in ensuring appropriate working environment. Exploring the business unit’s site with the basic question “what can go wrong?” Mitigating occupational safety risks.
Audits of high‑risk operations –improving the safety of hot and gas hazardous works, underground construction work, maintaining standards by means of audit based on a checklist for a certain type of work.
Briefings for each shift – daily awareness efforts for subordinate personnel to reiterate on hazardous factors and control measures prescribed when issuing a shift assignment before the start of a shift, admission to work in accordance with the expected types of work and planned production operations.
In 2023, as part of the transformation of safety culture and OHS management system initiative, the Company implemented Leadership in Safety Management, a programme of strategic sessions for N1–N3 managers.
Session objectives:
- to raise awareness of safety issues among N1–N3 managers;
- to shift from inspections and penalties to mentoring and proactive oversight;
- to build ability to deal with employee stereotypes and beliefs;
- to enable managers to show commitment to safety by personal example;
- to build understanding of leadership impact on safety culture;
- to be able to tell the difference between the notions of “leader” and “manager”;
- to develop a desire to influence safety culture and an understanding of how to do so.
Following an audit of the corporate work permit systems in place at the Cherepovets facility and Volkhov branch conducted in 2022, in 2023 the Company developed a target model of the work permit system to be rolled out across our assets as early as in 2024.