Supply chain
Area, strategic goals and metrics
Target 9.1
Further development of Process Mining and introducing new robotic solutions
Robert chatbot launched to quickly handle standard procurement queries
Migration of robotic solutions to a new Russian‑developed platform initiated
Target 12.4
Enhancing long‑term relationships with suppliers
- Long‑term agreements
- Consignment warehouses
- Online shops
Developing direct and alternative supplies of imported equipment and spare parts
2023 target: 30% of inventory
Increased procurement using embossed bank cards
Further development of category strategies
17 categories of materials and equipment
Target 8.3, 12.4 and 13.2
Training materials are available on the Company’s official website in the Procurement section
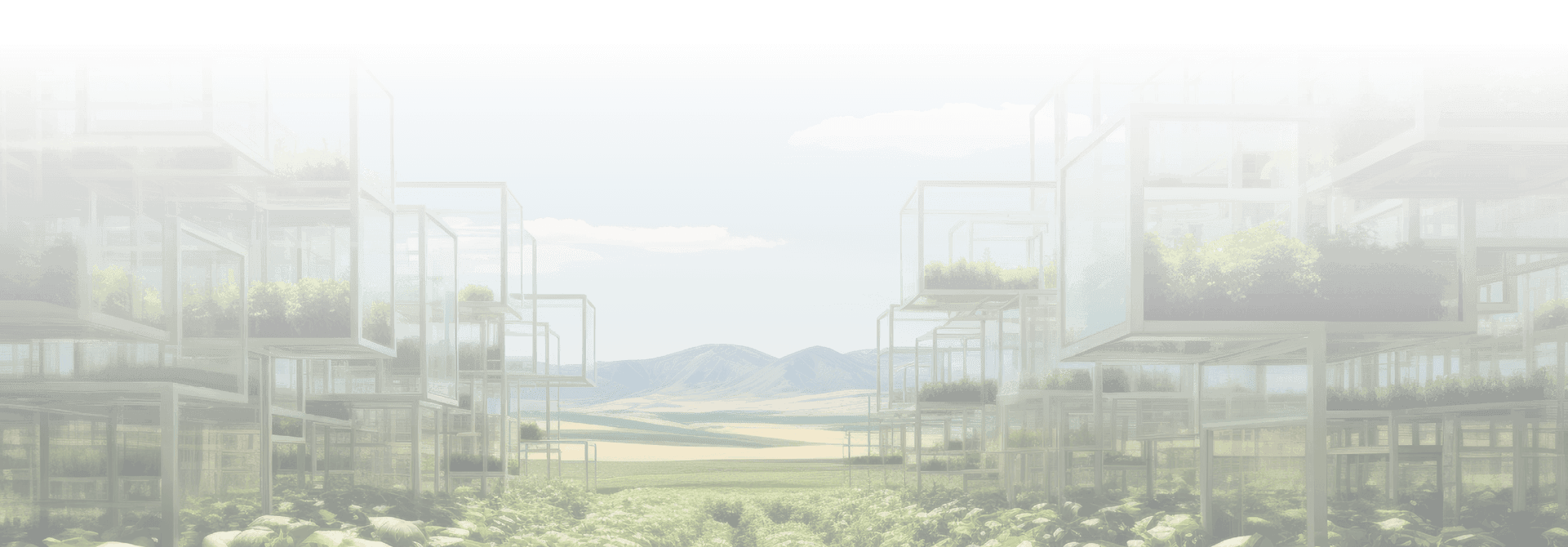
PhosAgro’s procurement system seeks to ensure that the Group’s subsidiaries receive the required resources, materials, and services of adequate quality in full and at reasonable prices. However, there is much more to the principles and business processes underlying our procurement activities. We believe that running a supply chain in an efficient and responsible manner is the cornerstone of the Company’s sustainable development.
In 2023, our procurements of goods and services reached almost RUB 184 bln. Thousands of our suppliers and contractors benefit directly from these investments, and so do their employees, who have to provide for their families. We contribute to the public budget at various levels. But what is more important is that the tools that we employ, including our environmental and social assessment of suppliers, as well as anti‑corruption mechanisms, directly promote sustainable values across the Russian business community. These values are the bedrock of our business philosophy. We work to ensure that our procurement activities have a strong positive impact on all our stakeholders.
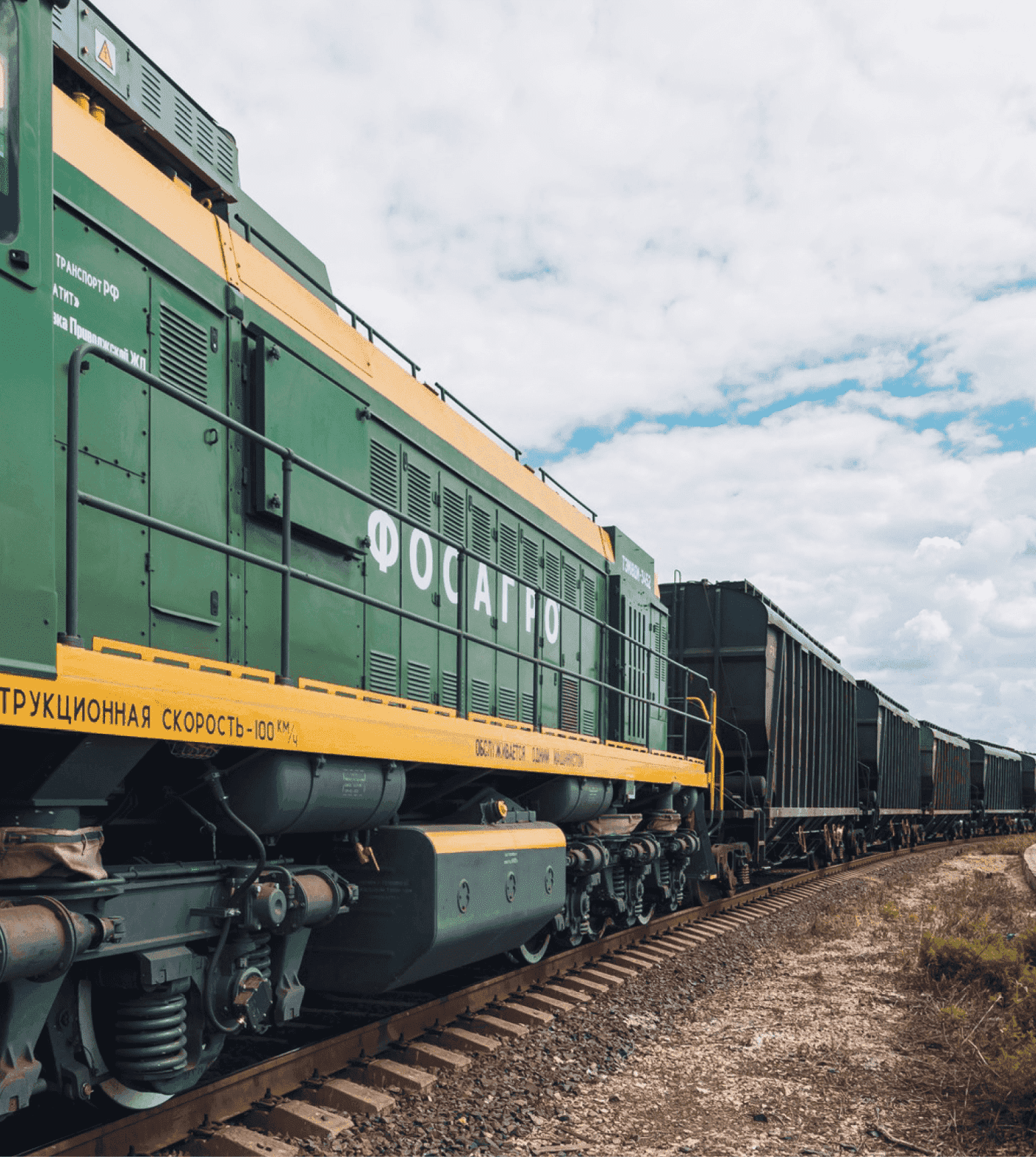
In its procurement, PhosAgro aims to foster open, trustful and mutually beneficial relationships with our partners in compliance with the applicable laws, regulations, and contractual and other obligations.
All of the Group’s suppliers, including potential ones, are subject to the Company’s anti‑corruption standards. To ensure compliance with Russian anti‑corruption laws and PhosAgro’s Anti‑Corruption Policy, prevent and fight fraud and corruption, avert conflicts of interest among PhosAgro employees, and provide more opportunities for companies and individuals to engage in supplies of goods and services in line with principles of good faith competition, transparency and openness, the Company adopts a zero tolerance approach to fraud and corruption in any form and manifestation. PhosAgro believes that any and all instances of bribery, fraud and corruption involving the Company’s employees and contractors are unacceptable. To enforce this principle, PhosAgro expects its potential contractors to meet certain obligations made known to them when first signing up to the EBP.
Documents governing the Company’s procurement activities are publicly available on its official website.
General information on PhosAgro’s procurement activities is available in the Procurement section on its official website
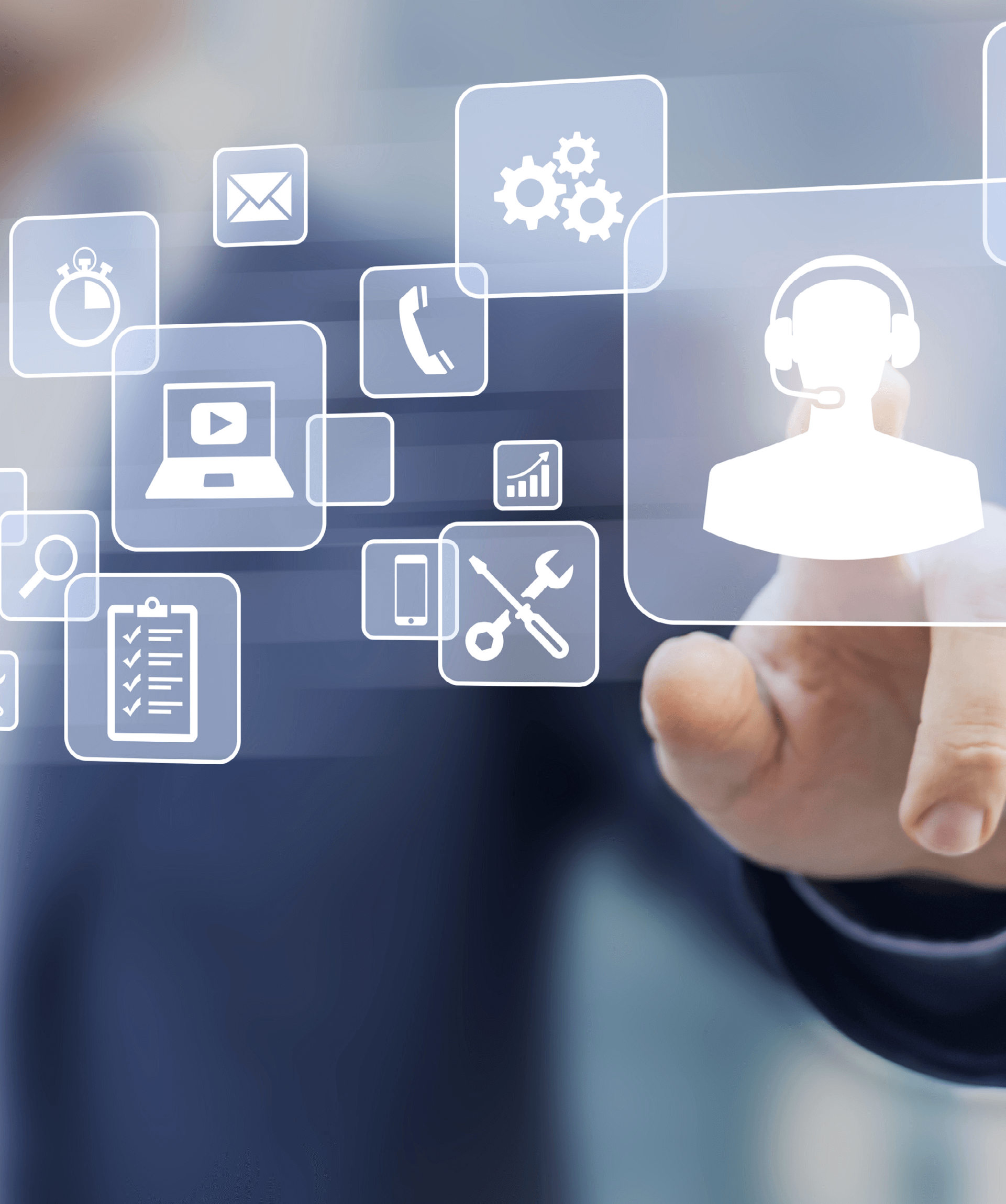
To assess the performance of its staff, the Procurement Department has individual KPIs in place aligned with the Company’s business goals. A development plan can be introduced at all levels in line with an employee’s or task group’s initiatives and projects, thus improving engagement and motivation.
KPIs contribute to better employee performance by creating a coherent vision of the deliverables and assessment criteria shared by the team and management. Progress against KPIs is regularly monitored, with interim evaluation in place. Overall performance of the Company’s procurement function is subject to annual review by PhosAgro’s Board of Directors.
The following strategic risks affect our procurement objectives
for more information, see the Strategic Risks section
Procurement‑specific risks are:
Сutting‑edge solutions to create optimal procurement models
The Company effectively implements cutting‑edge business solutions and IT tools in its procurement processes to create optimal procurement models and seamlessly interact with parties along the supply chain.
PhosAgro’s Hotline Regulations setting out the procedure for whistle‑blowing related to fraud, corruption, theft and conflicts of interest
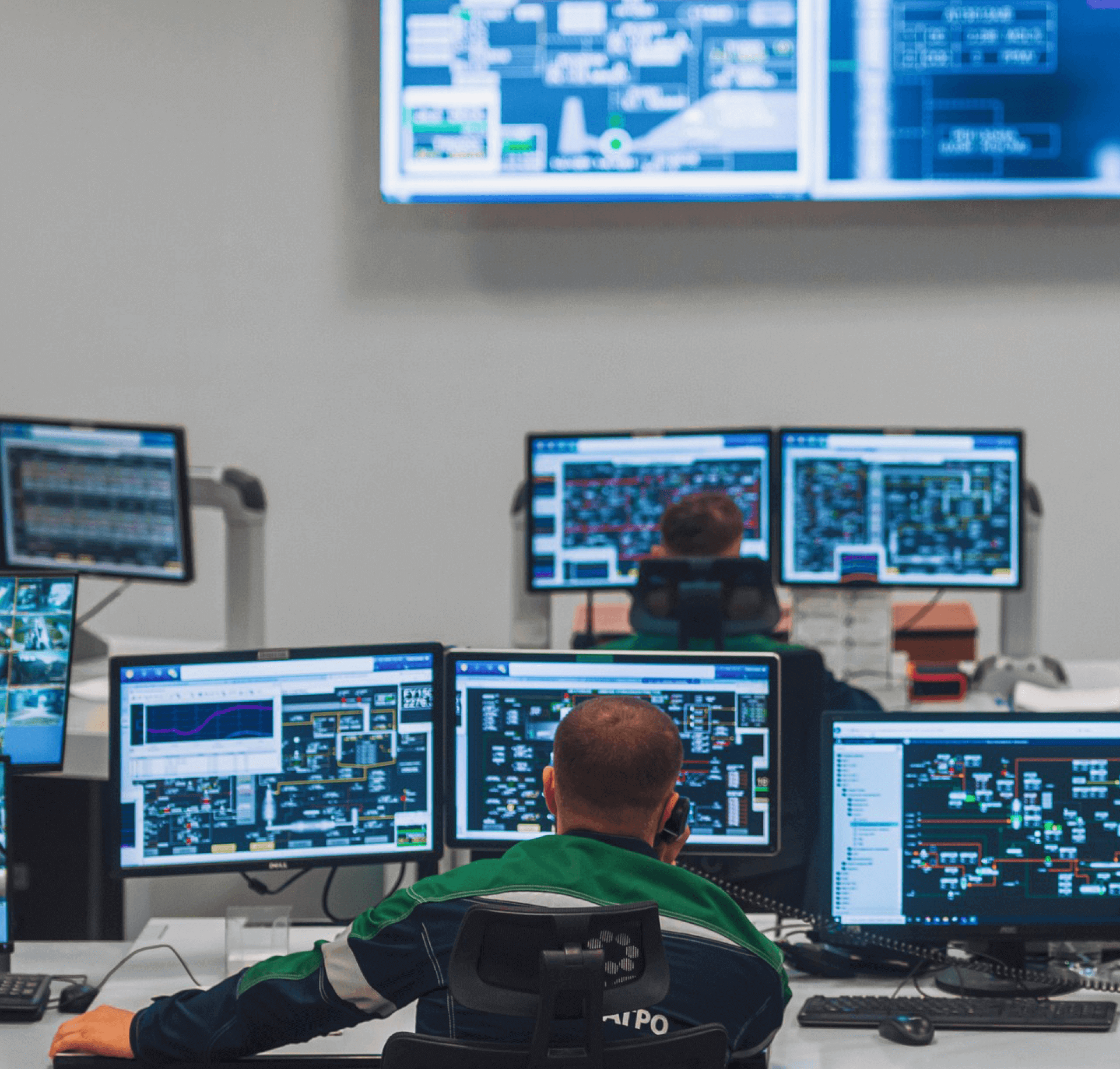
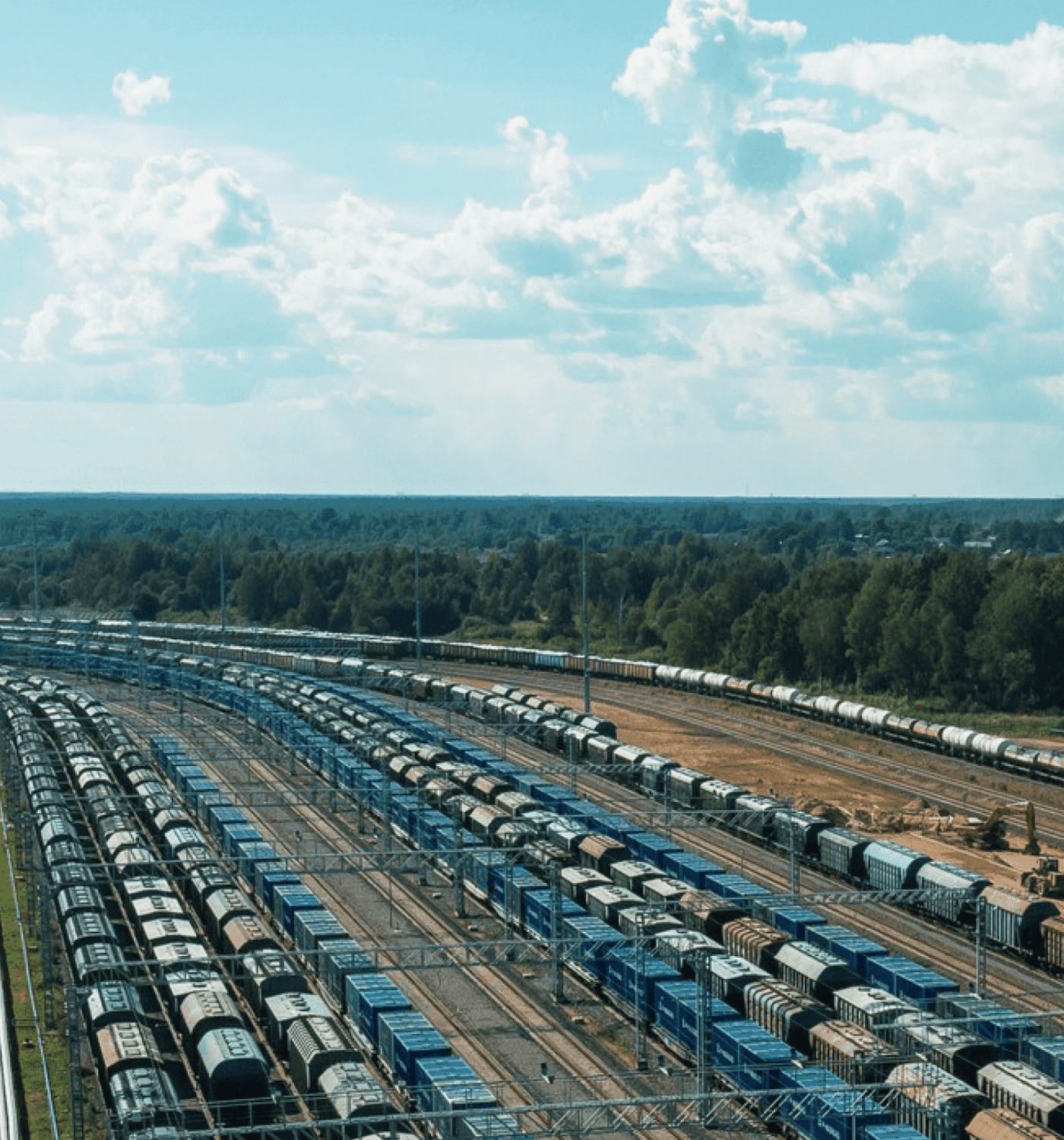
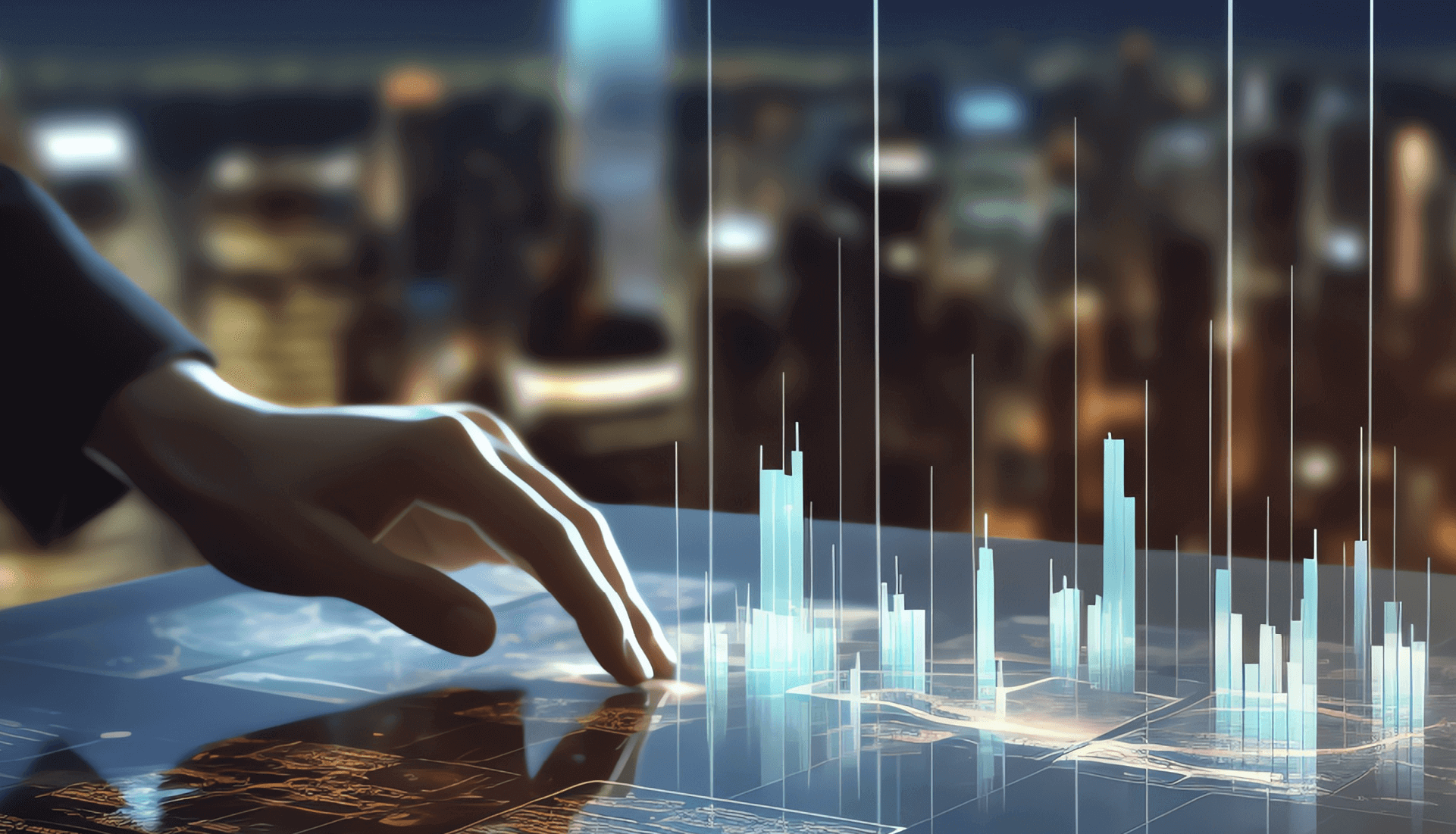
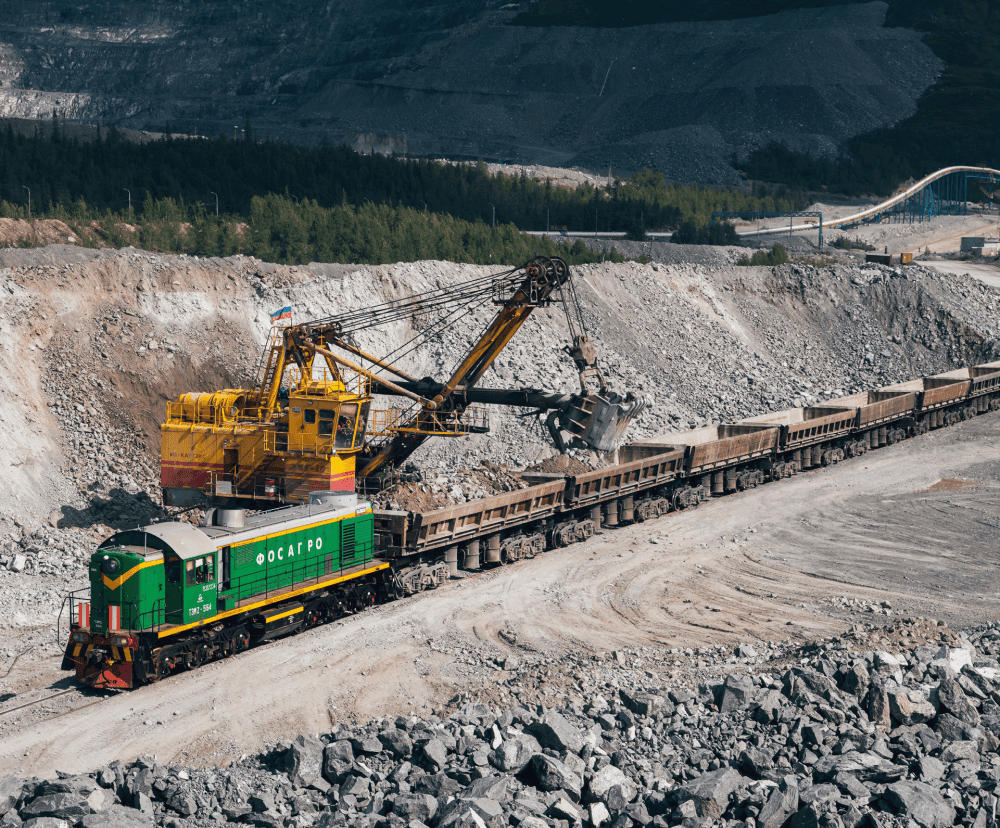
Cost budget
Geopolitical factors continued to have a significant impact on PhosAgro Group’s supply chains in 2023. Among other things, banking operations with foreign suppliers became more complicated. To respond to these challenges, PhosAgro introduced structural changes in the Procurement Department, organised alternative procurement, and put up new supply chains. Category managers secured timely supplies of materials and equipment that are critical for the operational process.
One of PhosAgro’s priorities was collaboration with Russian manufacturers, with a variety of trials held and agreements signed for long‑term cooperation and fine‑tuning of equipment (including self‑propelled underground machinery and automation and control equipment) to meet the needs of Apatit. To manage risks more effectively and swiftly, a dedicated flowsheet was introduced to monitor the supplies of critical inventory items. The insourcing of services provided by Cherepovets Energy Company helped increase the share of self‑procured electrical goods.
During the reporting year, PhosAgro achieved a further reduction in the reject rate at incoming control of centrally procured materials and equipment, bringing it down to 7.7% vs 8.7% a year earlier.
Digital tools
In 2023, PhosAgro’s Procurement Department continued to actively deploy digital tools and management solutions based on them. In particular, five robotic solutions were developed and implemented to administer and control tasks of procurement function, upload and verify documents, and select the approval route. In addition, the Robert chatbot was launched to quickly process typical procurement queries. At the same time, the transfer of robotic solutions to a new Russian platform was initiated as a way to improve reliability and efficiency.
In the reporting year, the expanded use of Process Mining technology reduced the time required to approve contractual documents by an average of 13%.
In 2023, PhosAgro’s EBP introduced a new functionality, the Document Management Form (DMF), which enables interaction with potential counterparties and automates the document collection on a one‑stop‑shop basis. Uploading and keeping documents in the DMF up‑to‑date are a responsibility of counterparties and a prerequisite for entering into contractual relations with Apatit.
In October 2023, PhosAgro Group won the Competitive Procurement Leader contest in the Procurement Digitalisation Leader category with its Procurement Automation and Internal Audit of Business Processes projects.
The Competitive Procurement Leader Award is the first professional competition in the field of trade and procurement, bringing together suppliers, government officials, mass media, and non‑governmental organisations. Established in 2012, the award aims to raise awareness about the most significant procurement projects that make operations of companies more efficient and transparent and contribute to the development of the market at large. In 2023, a total of 174 projects were submitted by companies across all industries.
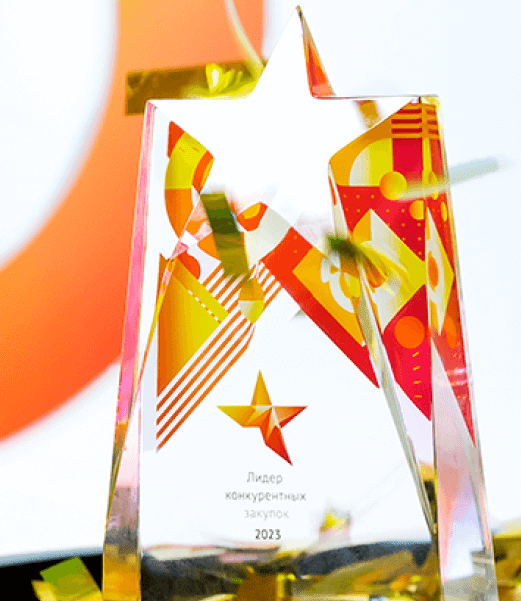
To inform and train its counterparties to use the DMF, the Company developed video instructions (available on PhosAgro’s official website).
Video instructions on PhosAgro’s official website
Video instructions in the Instructions section on PhosAgro’s EBP
In addition, the Company organised training for its counterparties as part of the Supplier Day and included links to the instructions in notices made available to counterparties registered on PhosAgro’s EBP.
The SCOUT system used to automate counterparty verification procedures was integrated with key corporate systems to collect and categorise data from corporate and external sources.

Improved performance
In the reporting year, PhosAgro focused on streamlining the operations of its Procurement Department and related joint ventures involved in the procurement process. To this end, we implemented a project to improve the efficiency of interaction between a joint‑venture customer and the Procurement Department by optimising end‑to‑end processes and structural changes, while another initiative – updating PhosAgro Group’s stock item catalogue – is now in the advanced stages of implementation. This has improved the operating efficiency of the Company units and enhanced the competences of employees involved in procurement, as well as helped us build universal chains of interaction between a joint‑venture customer (applicants) and the Procurement Department.
The Company also launched a project for the procurement of low‑value items on Marketplace, an online platform that connects suppliers and customers, which serves to reduce the transaction burden in non‑strategic procurement categories and increases the speed of B2B procurement.
Oleg Minnullin Head of Procurement, Apatit“Continuous development and improvement of business processes is the foundation that underpins everything we do in our function. We never stop learning and adopting the best practices of successful businesses.”![]()
Local supplier management
At the St Petersburg International Economic Forum in June 2023, the Company signed a protocol on the implementation of the cluster model of economic development in the Vologda region. This is a joint project of the regional government, Vologda regional branch of the Russian Union of Industrialists and Entrepreneurs (RSPP), PhosAgro Group, and Severstal. The initiative will see the creation of a new cluster model for the Vologda region’s economy at the industrial site in Cherepovets. The project of the Synergy of Growth 3.0 cluster model is a continuation of the Synergy of Growth project. It provides for the local manufacture of popular products in order to meet long‑term needs of the region’s largest businesses.
PhosAgro is also actively involved in similar initiatives organised by the Vologda regional branch of the RSPP and the All‑Russia Public Organisation Business Russia.
Suppliers are an essential aspect of sustainability in PhosAgro’s operations. The Company has an automated system in place to evaluate suppliers on the basis of ESG criteria, which results in an individual rating of each counterparty. This enables us to assess our suppliers’ environmental, social and governance performance.
To verify the resources and capabilities of its business partners, the Company conducts regular technical audits of suppliers. In 2023, we carried out 86 audits of Russian and foreign manufacturers, four of which were disqualified on the basis of environmental and social criteria.
Also, in order to unify approaches and criteria for evaluating suppliers, PhosAgro, as part of the National ESG Alliance, has been a member of a working group since 2023 to discuss draft unified supplier evaluation methodology, a practical ESG transformation solution for as many large companies as possible, as well as for medium and small businesses in corporate supply chains.
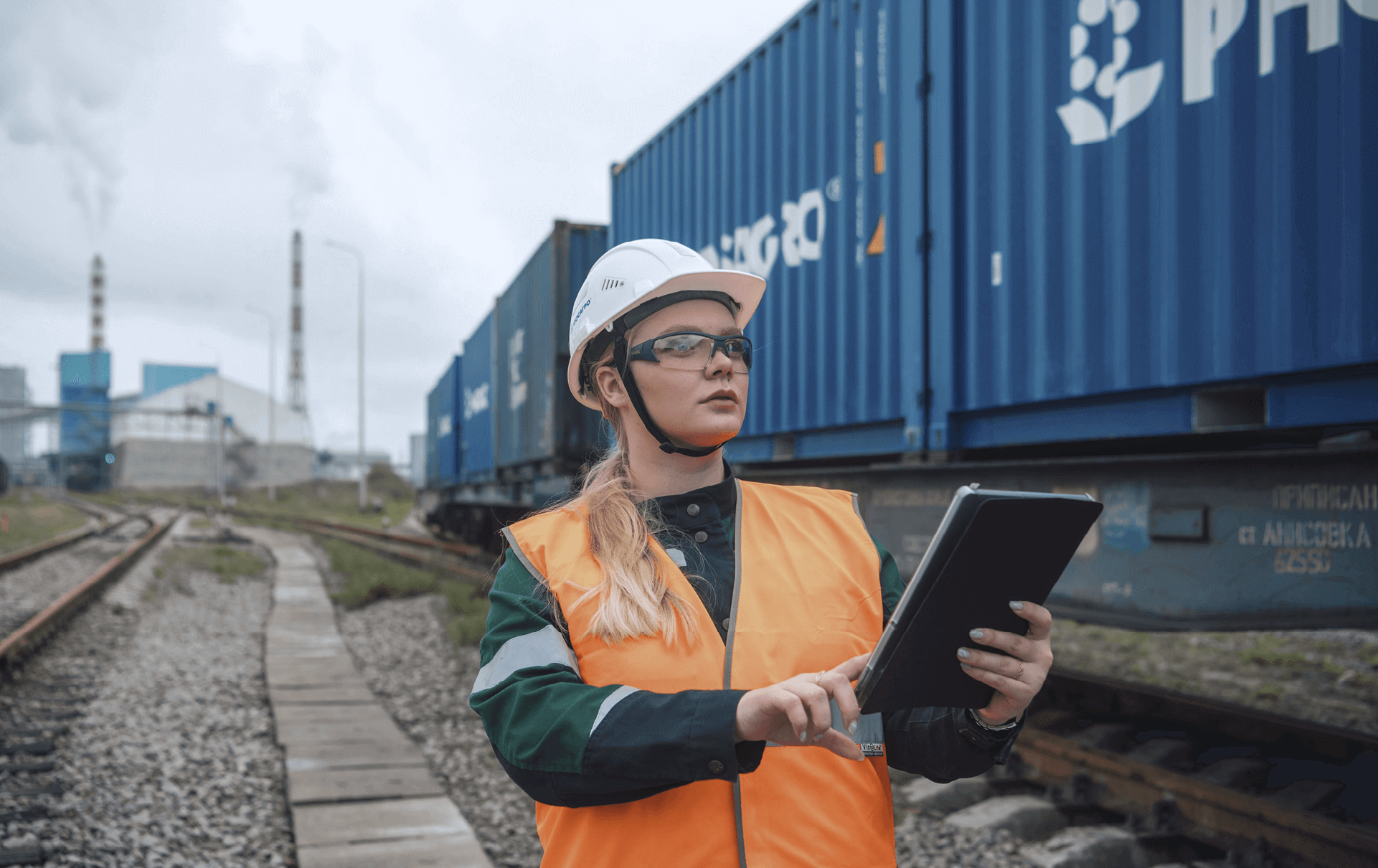
Key ESG evaluation indicators
In 2023, the total number of counterparties that underwent our ESG assessment based on their completion of the Sustainable Procurement Indicators checklist reached X (compared to X in 2022). The percentage of rated counterparties in total supplies increased from 35% in 2022 to 59% in 2023. The average score of suppliers also grew from 62 in 2022 to 65 in the reporting year.
Supplier environmental assessment
In 2023, more than a third of PhosAgro’s suppliers in the category “Raw materials, fuel, energy and commodities” had an environmental management system certified to comply with ISO 14001 or a similar standard (34% in 2023 vs 33% in 2022).
Supplier social assessment
According to the 2023 social assessment, 62% of PhosAgro’s rated suppliers adhere to the official zero‑tolerance policy on child labour. In addition, zero‑tolerance policies on discrimination and forced labour were adopted respectively by 60% and 61% of the Company’s counterparties in the categories “Producers of raw materials, fuel, energy”, “Commodity producers and intermediaries”, “Logistics services”, and “Construction and installation, repairs”. The share of counterparties in the above categories that have an occupational health and safety management system certified to comply with OHSAS 18001 or a similar system also rose to 40%.